ГХК для плазменного напыления
Компания Крионика ежегодно производит более трех сотен отгрузок. Так в прошлом году мы отправили клиентам более трёхсот сорока единиц продукции. Среди этих заказов есть и крупные, и небольшие, но важные. О самых интересных из них мы пишем статьи. Если в статье вы узнаете соседа или конкурента, имейте в виду, мы помогли им улучшить свое производство. Среди заявок, поступивших в этом году, хочется отметить запрос от Уфимского предприятия по ремонту газотурбинных установок. Целью было обеспечить производственный цикл газообразным аргоном. Для ремонта турбин используется метод плазменного напыления в среде аргона: защитное вещество подается в плазму и в среде аргона наносится на лопатки турбины.
Популярный при работе с аргоном способ хранения его в баллонах не подходил по нескольким причинам:
- Требуется большое количество газа. Если смотреть в баллонах, то не менее 30 штук(в наличии на производстве). Обслуживание парка баллонов – трудоемкая задача. Необходимо найти производственные площади, обеспечить своевременное переосвидетельствование и хранение в соответствии с нормами промышленной безопасности.
- Технологический процесс плазменного напыления требует стабильного состава смеси. К примеру: первая деталь из партии проходит контроль. Чтобы подтвердить качество всей партии деталей, условия производства должны быть аналогичны. Состав аргона, который поставляется продавцами технических газов, отличается в рамках партии баллонов. Он может быть влажным, с мусором, окислами, с пылью. Это значит, что нужно постоянно контролировать состав газа и перенастраивать оборудование, если обнаружены изменения. Кроме того, если не выявить отклонение вовремя, часть деталей попадет в брак.
В результате, даже если клиент решит проблему с площадью и хранением, нестабильность состава приведет к увеличению длительности и стоимости ремонта.
После погружения в предоставленный клиентом технологический процесс предложено решение: Газификатор ГХК 1,0/1,6-60.
Чтобы рассчитать параметры оборудования, мы отталкивались от следующих ключевых моментов производственного процесса:
- Объем газификатора. Важно подобрать объем, достаточный для нужд производства. Таким образом можно оптимизировать заправку газификатора, сократить трудозатраты и избежать лишних остановок технологического процесса. Слишком маленький газификатор потребует ежедневной заправки. А слишком большой объем сосуда может привести к постепенному рост давления и потере рабочего газа через предохранительную арматуру.
- Рабочее давление. Параметр, определяющий тип сосуда. Исходя из рабочего давления, определяется диапазон давлений, допустимых для технологического процесса потребителя. Рабочее давление газификатора должно быть на несколько атмосфер выше давления в сети потребителя.
- Расход. С помощью этого параметра определяется производительность газификатора.
По предварительным расчётам клиенту подходил ГХК 1/1,6-30 со следующими характеристиками:
Объем сосуда – 1000 л;
Рабочее давление – 1,6 МПа; Расход – 30 м3/ч.
По запросу клиента мы провели дополнительный расчет, и, чтобы обеспечить двойной запас производственной мощности, остановились на ГХК 2/1,6-60. (Рисунок 1)
Остановимся на выбранном варианте подробнее. ГХК 2/1,6-60 это сборный газификатор. Он состоит из следующих основных агрегатов:
- 4 сосуда типа DPW650-499-1.6 (Рисунок 2);
- рампа выдачи РР 01-04-40 (Рисунок 3);
- продукционный испаритель ИА 40-060 (Рисунок 4);
- общая линия заправки (Рисунок 5).
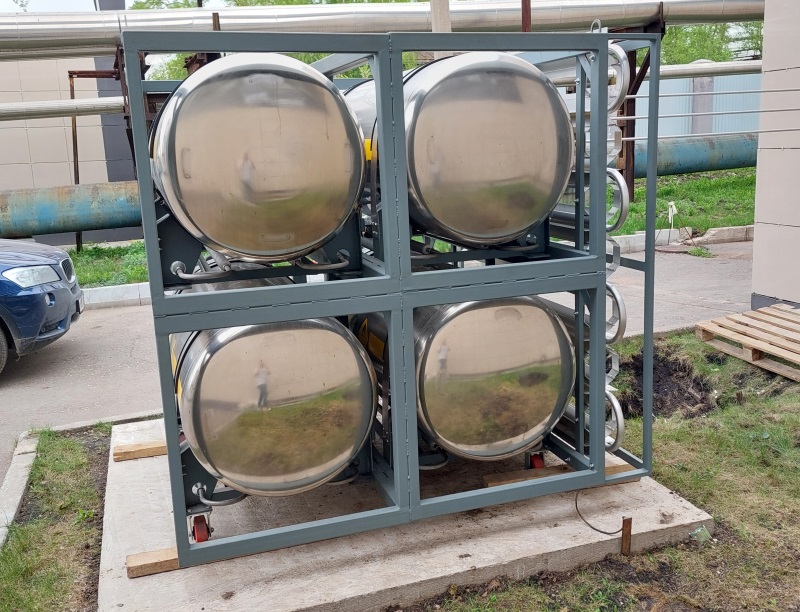
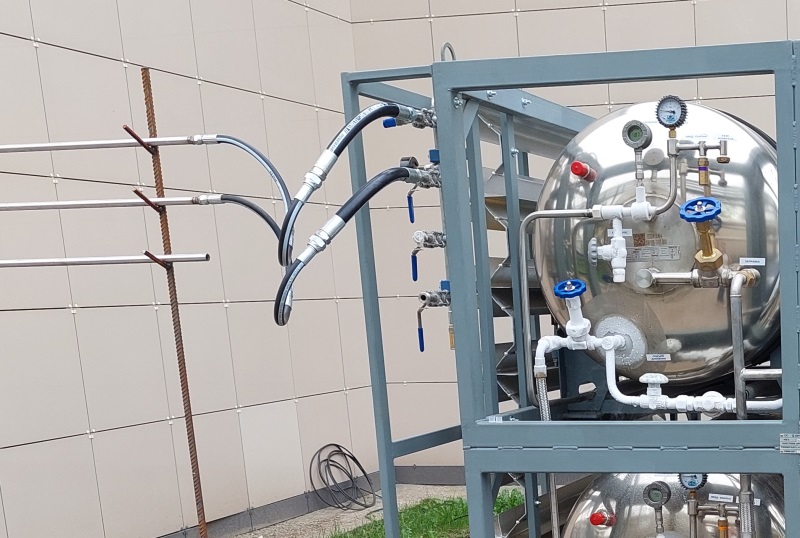
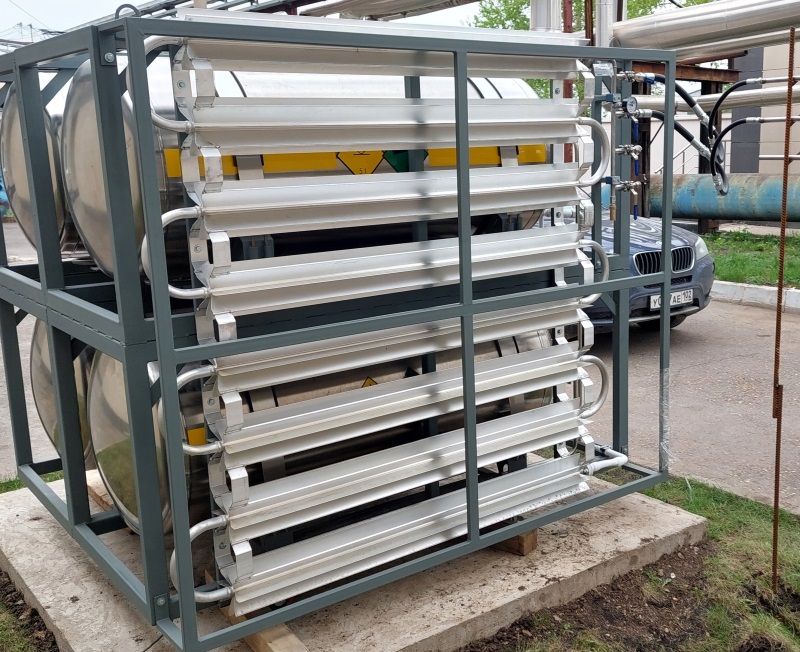
При необходимости можно изготовить данную емкость большей производительности. В нашем случае этого не требовалось, и конфигурация подбиралась исходя из комфортного для клиента объема хранения продукта. В данном изделии потери продукта составляют менее 2%(двух процентов) в сутки от общего объёма хранения. Этот показатель напрямую влияет на частоту заправки и помогает сократить трудозатраты на неё.
Среди прочего, клиент решил воспользоваться дополнительными услугами, которые предоставляет ООО "Крионика", а именно:
- доставка до адреса производственного объекта в городе клиента;
- рассрочка платежа с авансом всего в 50% от стоимости изделия;
- настройка жидкостного уровнемера;
- настройка регулятора подъёма давления (Feilun DYS-06F115);
- комплект запасных частей сосуда (Предохранительный клапан, клапан подъёма давления, Манометр).
Рассмотрим подробнее конструктивные особенности газификатора.
За основу взяты 4 сосуда DPW650-499-1.6 производства бренда Runfeng. Для необходимой жесткости конструкции, она размещена на сварной раме. На ней размещены проушины, которые позволяют транспортировать изделие краном. Испаритель защищен от механического воздействия специальной рамой. Рампа размещена в верхней части конструкции. Так изделие становится более эргономичным, т.е удобным для работы оператора. Чтобы унифицировать общую линию заправки, в качестве заправочного порта выбрана Гайка РОТ.
К Гайке Рот 40 приварена труба ДУ40, которая далее разветвляется на 4 трубы диаметром 25 мм. Такая конструкция помогает ускорить заправку газификатора, ликвидирует узкие места в трубопроводе и снижает потери рабочей среды при заправке. Трубопровод заправки содержит 3 гибких рукава, чтобы компенсировать температуру при захолаживании. Также он разборный, что повышает его ремонтопригодность (Рисунок №6).
Газификатор изготовлен из комплектующих и арматуры, которая была в наличии на складе. Поэтому он был изготовлен всего за 12 дней. Широкий ассортимент криогенной арматуры помогает нам не только сократить срок производства, но и обеспечивать гарантийные обязательства и постгарантийные услуги.
Когда изделие прибыло к клиенту, он сам осуществил захолаживание и заправку газификатора. Далее на предприятие прибыл наш специалист для ввода изделия в эксплуатацию. К моменту прибытия газификатор был заправлен 4 дня. Наш специалист провел инструктаж и подготовил персонал клиента к работе с газификатором, дал рекомендации по оснащению. Также, он настроил регуляторы подъема давления, чтобы в работе всегда находились 2 емкости из 4. Остальные емкости будут в резерве и автоматически подключатся к работе при опустошении первых 2х. Чтобы оставить запас для естественного роста давления, емкости настроили на давление 6 кгс/см2 и 8 кгс/см2 при рабочем давлении 4 кгс/см2.
Вместе с изделием клиенту предоставлен пакет технической документации, в который вошли:
1. Паспорт криогенного сосуда
2. Инструкция по эксплуатации сосуда
3. Паспорт предклапана сосуда
4. Паспорт предклапана рампы на сосуде
5. Формуляр газификатора
6. Паспорт и инструкция по эксплуатации испарителя
7. Инструкция по эксплуатации уровнемера
8. Паспорт и инструкция на рампу
8.1. Паспорт манометра сосуда
8.2. Паспорт манометра рампы
9. Паспорт и инструкция по эксплуатации вентиля заправки
10. Паспорт и инструкция по эксплуатации вентиля газосброса
11. Паспорт и инструкция по эксплуатации вентиля выдачи жидкого продукта
12. Паспорт и инструкция по эксплуатации вентиля подъема давления
13. Паспорт и инструкция по эксплуатации регулятора подъема давления
Подведем итог и попробуем оценить правильность выбора поставленного изделия.
Клиенту необходимо было обеспечить давление в системе не менее 14 бар при расходе 30 м3/ч. Для этой задачи мог подойти сосуд ГХК 1/1,6-30. Это газификатор объёмом 1000л, который вмещает 1324кг аргона. С его помощью можно было соблюсти оптимальный режим работы с периодичностью заправки 1 раз в 7 рабочих дней. Массово-габаритные характеристики ГХК 1 позволяют перевозить его в обычном авто класса N1. Количество выходов газа – 4, как и у ГХК 2.
Почему в данном случае выбор пал на ГХК 2? Все дело в объеме хранимого газа. Аргон один из самых дорогих газов на рынке. Его средняя стоимость 180 руб/кг, в то время как у Азота – 25руб/кг. При заправке от 2 тонн поставщик технических газов, как правило, даёт существенную скидку. Если умножить скидку на количество заправок в год, получается ощутимая экономическая выгода.
При выборе оборудования мы учитываем не только необходимые технические характеристики, но и особые требования заказчика. В данном случае частота и объем поставки газа. Если вы работаете с газами, хотите оптимизировать свое производство и получить индивидуальный подход, звоните или пишите Нам. Мы с радостью поможем вам.